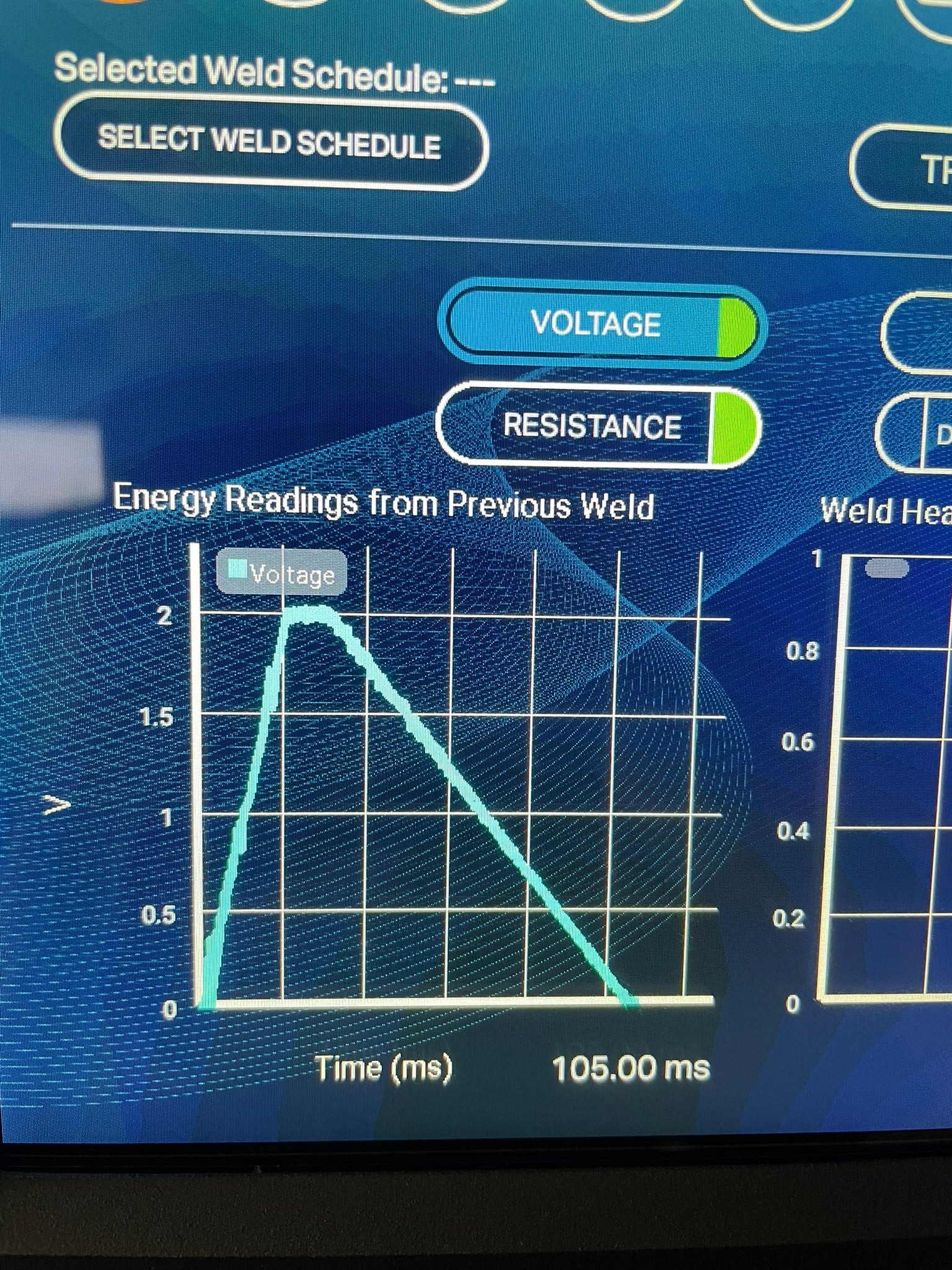
Weld Around the World with the Sunstone Wave AC® Resistance Welder
The Sunstone Wave AC resistance welder represents a significant advancement in precision welding technology, delivering 2,700 amperes of power through its sophisticated electronic control system. This industrial-grade welder combines advanced transformer technology with digital precision controls, enabling manufacturers to achieve consistent, high-quality results across diverse applications.
From seam welds on mesh and foil welding to filter production and spot welding, the Wave AC's capabilities extend across multiple industries, offering solutions for complex welding challenges. Significant features include:
- The system's 10-inch touchscreen interface and waveform visualization features provide operators with unprecedented control over welding parameters.
- State-of-the-art transformer design ensures optimal energy distribution for superior weld quality.
With this article I will examine the Wave AC's technical specifications, practical applications, and the technology that sets it apart in modern manufacturing environments.

Introducing the Sunstone Wave AC®
The Sunstone Wave AC resistance welder delivers exceptional performance through its powerful 2,700 ampere output capacity and sophisticated electronic control system. As an industrial-grade welder, the Wave AC meets the demanding requirements of manufacturers who require precise, repeatable welds across various materials and thicknesses.
The Wave AC's core capabilities include:
- High-precision AC output control
- Advanced seam welding functionality
- Integrated wheel electrode compatibility

"Weld Around the World" with Seam Mode and a Wheel Electrode
The Wave AC's seam mode, combined with its wheel electrode compatibility, enables continuous welding operations essential for manufacturing processes. This feature allows operators to create consistent, uninterrupted welds along extended material lengths, no matter the shape or design, making it ideal filter assembly, and mesh welding.
Key seam welding capabilities include:
- Precise control of weld spacing and overlap
- Roll Spot mode and Continuous Seam Mode
- Visualization of weld parameters
- Easy energy adjustment during operation
Digital Control System Transforms Welding Precision
The Wave AC's 10-inch touchscreen interface transforms welding operations through real-time visualization and precise digital control. Operators can monitor and adjust welding parameters through an intuitive display that shows active waveform patterns, energy distribution, and timing sequences.
The digital control system offers:
- Visual waveform monitoring and adjustment
- Precise parameter control with numerical inputs
- Stored welding profiles for consistent results
Advanced Transformer Technology Delivers Superior Results
The Wave AC's transformer incorporates advanced magnetic core materials and precision-wound coils that optimize energy transfer efficiency. This sophisticated design enables precise control over current delivery, maintaining consistent power output throughout the welding cycle.
Key technological features include:
- High-frequency switching components for rapid energy adjustment
- Advanced thermal management system
- Integrated power factor correction
- Real-time impedance monitoring
The transformer's electronic control system continuously monitors and adjusts power delivery based on material resistance changes during welding. This dynamic response system ensures optimal energy distribution, resulting in superior weld strength and consistency across various material combinations. The system's ability to maintain precise current levels throughout the weld cycle reduces material distortion and improves overall weld quality.
Optimal Applications and Industry Solutions
The Wave AC resistance welder excels in multiple industrial applications, particularly in manufacturing sectors requiring precise, repeatable welding processes. Its capabilities directly benefit filtration industries, aerospace component assembly, and battery manufacturing operations.
Primary applications include:
- Battery assembly welding
- Aerospace instrument manufacturing
- Filter mesh production
- Automotive sensor assembly
- Thin foil welding operations
In aerospace manufacturing, the Wave AC's precise control enables consistent joining of sensitive components. For filtration production, its seam welding capabilities ensure uniform connections across mesh to mesh, and mesh to solid metal assemblies. The system's advanced control features improve manufacturing efficiency by reducing setup time and minimizing material waste while maintaining strict quality standards.
The Wave AC resistance welder delivers 2,700 amperes of maximum output power through its advanced transformer system. Operating on standard 208-240V single-phase power, this industrial system maintains precise control across its full power range.
Technical specifications include:
- Input voltage: 208-240V AC
- Maximum output: 2,700 amperes
- Display: 10-inch color touchscreen
- Weld modes: Spot, seam, and continuous
- Dimensions: 24" x 18" x 12"
- Digital parameter control: 0.1ms precision
- Memory storage: 100+ weld profiles
The system's integrated thermal management and power factor correction technology enable extended operation periods while maintaining consistent output quality. These features, combined with its digital control capabilities, distinguish it from conventional resistance welders that lack precise parameter adjustment and monitoring functions.

FAQs for the Wave AC®
Here are essential questions and answers about the Wave AC resistance welder:
What routine maintenance does the Wave AC require?
Regular electrode cleaning and inspection are the most important. Other maintenance checks can include quarterly overall machine inspection and cleaning, and annual visual and resistive checks on welding cables. Clean cooling vents monthly to prevent overheating.
How do I program welding parameters?
Access the parameter menu through the 10-inch touchscreen. Input values for Power Step (1-4), percent of phase, number of phases, and spot mode or seam mode. Save custom profiles for recurring operations. The system stores over 100 weld configurations.
What technical support is available?
Sunstone provides remote diagnostics, on-site service, and comprehensive training programs. Technical support specialists assist with parameter optimization and troubleshooting via phone or email.
How often should electrodes be replaced?
Resurface electrodes when visible wear affects weld quality, or when material starts sticking to the electrodes. Keeping the electrodes clean, and smooth, with even wear, will help the welds maintain the best quality.
Can the Wave AC integrate with automated systems?
The system supports integration with robotic welding systems and automated production lines through standard industrial protocols. Coordinate with technical support for specific implementation requirements.
Text or Call +1 801-658-0015