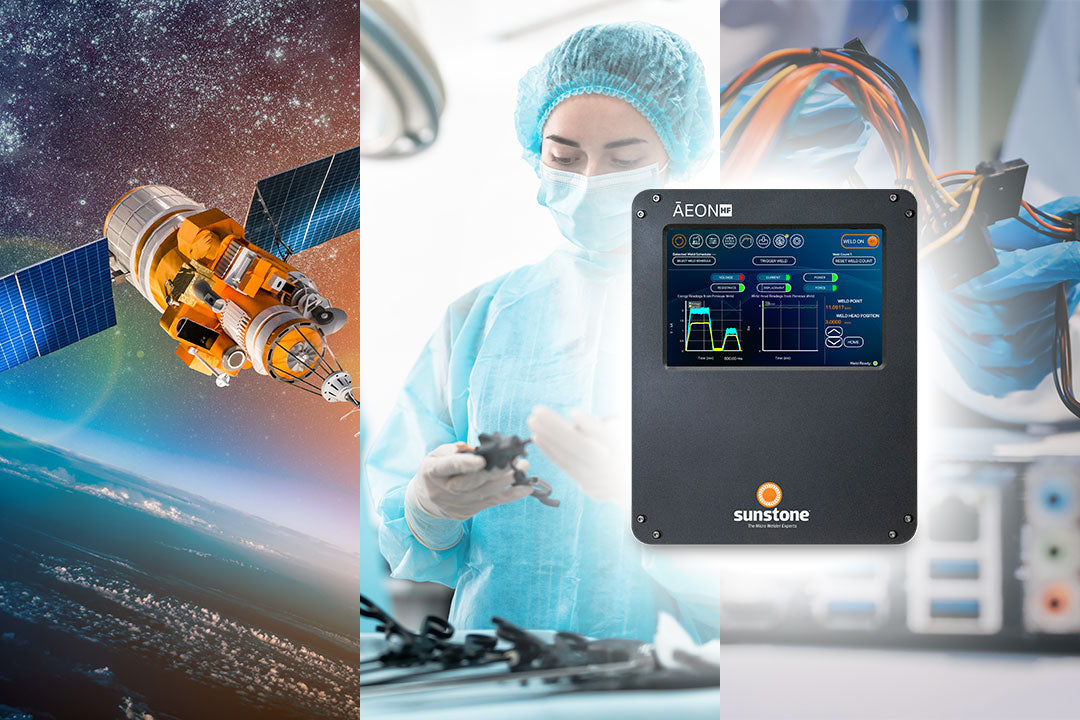
Pioneering High-Frequency Inverter Welding in Modern Manufacturing with the Sunstone Aeon HF
Sunstone's legacy in precision welding technology shows a deep understanding of material joining processes and a dedication to advancing practical applications of resistance welding through continuous innovation.
The latest in this lineage, the Aeon HF Inverter, embodies significant advancements in high-frequency (HF) inverter welding technology, combining both functionality and sophistication within a compact, self-contained system. In this article, I'll examine the scientific underpinnings and technological advancements of the Aeon HF, emphasizing its unique integration, precise control, and automation potential.
This is Not Your Father’s HF Inverter
Traditional HF inverter welders have long been preferred in applications that demand high-speed, controlled energy output, offering greater accuracy compared to conventional AC and DC systems. However, the Aeon HF Inverter elevates these capabilities, introducing unprecedented fine-tuning for weld energy management through a sophisticated user interface.
The all-digital touchscreen interface allows the operator to set precise parameters and, critically, modify them in real time. The scientific breakthrough here lies in the precise waveform modulation, enabling both amplitude and frequency adjustments that improve weld control across a spectrum of material resistances and thicknesses.
Another notable advance is the system’s compatibility with a range of automation protocols—from Basic PLC I/O and Modbus via Ethernet to RS-232. These protocols facilitate not only real-time adjustments but also remote monitoring and control, ideal for integration into complex production environments where seamless data communication is vital. The Aeon HF’s modern design isn’t merely aesthetic; it embodies an ergonomic approach to simplify machine setup and operation, thus enabling operators to achieve high precision with minimal interaction.
All-in-One Design
One of the most groundbreaking aspects of the Aeon HF Inverter is its consolidated, all-in-one design. In contrast to traditional HF systems, which require separate units for specific tasks, the Aeon HF houses all critical components within a single architecture. This integration is a significant achievement in both design and functionality, reducing the need for inter-module communication and thereby improving response times and accuracy.
Within this singular unit, the Aeon HF incorporates weld head control, force monitoring, and displacement monitoring functions, each essential to precise weld control. Additionally, the unit provides comprehensive current, voltage, power, and resistance monitoring for the power control. These monitoring capabilities enable a precise feedback loop— creating a closed-loop system that responds dynamically to changes in material behavior under heat.
The inherent advantage here is the system’s ability to self-correct, minimizing weld defects due to variances in material conductivity, thickness, or surface conditions. This tightly integrated design streamlines calibration processes and ensures a coherent, accurate setup, particularly beneficial for advanced research and industrial applications.
By unifying all these functionalities in a single compact system, the Aeon HF minimizes the spatial footprint, reduces setup time, and removes potential points of failure associated with multi-unit configurations. This scientific achievement in hardware integration is complemented by the Aeon HF’s robust software architecture, which facilitates streamlined adjustments and seamless monitoring from one central interface.
High-Volume Production and Automation
The increasing demand for high-volume production has pushed welding technology toward greater automation and control capabilities. From microelectronics and aerospace to automotive and medical device manufacturing, industries are driven by a need for high throughput while ensuring precision and consistency. Sunstone’s Aeon HF meets these requirements by offering built-in automation compatibility, thus allowing it to operate as part of a sophisticated production line with minimal manual intervention.
The Aeon HF’s automation-ready features include Basic PLC I/O functionality, Modbus via Ethernet, RS-232, and a remote schedule select option. These connectivity options permit seamless integration into automated environments, enabling the Aeon HF to operate as an integral part of robotic cells or automated weld stations. By providing multi-layered automation access, Sunstone ensures that the Aeon HF is adaptable to various production scenarios, from high-speed electronics assembly to repetitive medical device manufacturing.
The remote scheduling feature, in particular, is scientifically significant, as it allows operators to predefine weld parameters for multiple applications, effectively creating a digital “recipe book.” This capability minimizes the downtime required for manual parameter adjustments and ensures consistency across batches—critical for applications that demand uniformity and high reliability.
Paired with the Pro E Weld Head – Maximum Weld Control
The Aeon HF’s performance reaches its pinnacle when paired with Sunstone’s Pro E Weld Head, available in both opposed and parallel configurations. This weld head is engineered with a focus on achieving micron-level accuracy in weld placement, a critical requirement in high-precision applications. With 1-micron movement accuracy, the Pro E Weld Head sets a new standard in precision control, making it indispensable for tasks where even the smallest deviation can impact product quality.
In addition to precision movement, the Pro E Weld Head provides force monitoring and displacement monitoring capabilities. These features are paramount in establishing a stable, repeatable welding process, especially for delicate materials or assemblies. By dynamically monitoring force and displacement, the Aeon HF-Pro E combination achieves near-zero variation in weld quality across production runs. This pairing exemplifies Sunstone’s commitment to integrating advanced scientific principles into practical welding applications, enabling users to precisely control the weld dynamics at every phase of the process.
Advantages of HF Resistance Welding
In welding science, the advantages of HF inverter resistance welding over CD (Capacitor Discharge), AC (Alternating Current), and DC (Direct Current) resistance welding are well-documented. HF inverter welding systems, such as the Aeon HF, are distinguished by their ability to deliver high-frequency, continuous energy with minimal power loss. This stability allows for fine-tuned control over weld penetration and heat distribution, which is especially valuable in applications requiring minimal thermal impact on surrounding materials.
While CD welding offers quick energy release suitable for thin or fragile materials, it does not provide the extended energy control possible with HF inverters. AC welding systems, by their nature, are limited in frequency control, leading to potential inconsistencies in weld penetration and surface finish. Although DC welding provides more consistent energy output, it lacks the rapid response and fine adjustment potential inherent in HF systems.
The Aeon HF Inverter exemplifies the advantages of HF technology by enabling precise waveform control and energy delivery. This capability is critical in applications such as micro-welding or thermally sensitive assemblies, where even slight fluctuations can compromise the weld’s integrity. The scientific community recognizes HF inverter technology as the preferred choice for applications demanding precise thermal control, minimal spatter, and reduced heat-affected zones. Consequently, industries ranging from medical device manufacturing to aerospace can greatly benefit from the Aeon HF’s HF inverter capabilities.
Conclusion
The Sunstone Aeon HF Welder stands as a sophisticated synthesis of cutting-edge HF inverter technology, automation compatibility, and a thoughtfully engineered, all-in-one design. This welding system addresses both current and emerging challenges in precision manufacturing, equipping users with the control necessary to achieve exacting standards in high-volume, automated environments. Its compact, unified design offers a practical solution to the typical complexities of multi-unit systems, combining ease of use with scientifically validated precision and reliability.
By combining the Aeon HF with the Pro E Weld Head, Sunstone has established a new standard in HF resistance welding, one that caters to industries where precision, control, and automation are paramount. The AEON HF Inverter is not just a welding solution but a testament to the advancements in welding science—one that enables manufacturers to achieve results previously thought unattainable.
Test Your Work Piece with the Aeon HF™
As an essential tool for any high-precision manufacturing environment, the Sunstone Aeon HF Welder is poised to advance production capabilities, improve weld quality, and streamline operations. To explore how the Aeon HF can meet the exacting demands of your applications, ask a Sunstone micro welding consultant about our complimentary samples program: Send us a sample and we'll find the best welding solution.